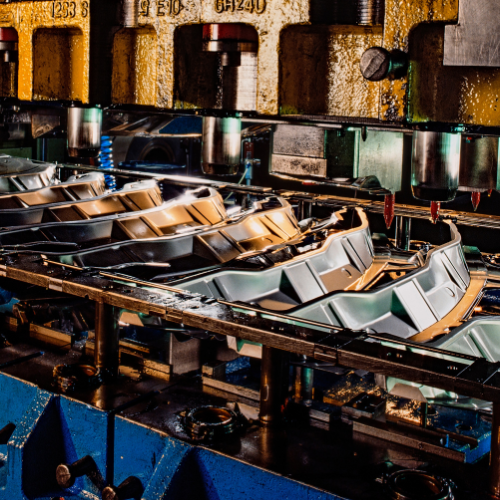
Types of Sheet Stamping Dies
Sheet Metal stamping is the process of shaping flat metal sheets (called blanks) into specific shapes and sizes to produce various components, usually for vehicles. This process involves the use of a stamping press and a die set, which is designed to shape the metal sheet into the desired shape, and a metal stamping press. Basically, to turn sheet metal into custom parts. Metal stamping is common in a few industries but is most prevalent in the Automotive industry.
Overview of Different Types of Dies and Stamping Techniques
Several types of dies are used in sheet metal stamping, each with specific capabilities and applications. Some of the most common types of dies include tandem dies, progressive dies, transfer dies, compound dies, fineblanking dies, draw dies, and trim dies. All dies are similar, in that, they turn the flat blank into complex parts using common processes such as bending, punching forming, embossing, blanking and deep drawing to produce custom stamped metal parts. This can be done with multiple station dies, combination dies, or any other type of dies. It depends on lead time, material thickness, the precision needed, press availability, type of steel etc. Some parts can be done in a single press with a single stoke to create parts. Other complex parts may need multiple steps or even off-line tools.
Each die type has its unique design and capabilities, making it ideal for specific applications in the metal stamping industry. Understanding the different types of dies and their capabilities is essential for selecting the best die for a specific application.
There are many things to consider prior to creating a die to stamp out parts. These are complex projects with varying quality specifications. Firstly, when the data is sent to a Tool and Die shop, they look at the computer aided design (CAD) of the component. Usually from that point, they will usually bring it into simulation software, like AutoForm and see how many operations they will need to create this custom component. Material thickness and material type is a big driving force behind the tonnage of the press or presses that will be needed.
This article will provide an overview of the various types of dies used in sheet metal stamping, including their definitions, advantages, and applications.
II. Progressive Dies (Progs) in Metal Stamping
Progressive die stamping is a type of metal stamping to process that are designed to perform multiple operations in a single pass through stamping presses. The metal sheet is progressively advanced through the die, undergoing various operations such as punching, cutting, bending, and forming until the final product is produced. This results in a more efficient and cost-effective process compared to using multiple stamping dies for each operation.
Advantages of Using Progs
Increased efficiency: By performing multiple stamping operations in a single pass through the stamping press, the production process becomes more efficient, reducing the overall time required for each operation. The sheet metal material is in a coil normally so you do not need a blanking die for these projects.
Improved accuracy: Progs are designed to perform multiple operations in a specific order, which helps to ensure that the final product is accurate and consistent.
Cost savings: By reducing the number of die sets required, progs can help to lower overall production costs. Especially if the part needs a deep drawing process as material will be saved by using a coil instead of blanks.
Applications of Progs in flat Sheet Metal Stamping
Body panel stamping: Commonly used in the production of automotive body panels, where they are used to cut, bend, and form coil into the desired shape.
Chassis components: Can also be used in the production of various chassis components, such as cross members, brackets, and sub-assemblies.
Engine components: Used in the production of engine components, such as cylinder heads, intake manifolds, and valve covers.
Progs play a significant role in the metal stamping industry and provide numerous benefits to manufacturers and suppliers. Performing multiple operations in a single pass through the press offers increased efficiency, improved accuracy, and cost savings, making them a preferred choice for many applications in the automotive industry. If it can be done by progressive die stamping operations, it should be. Many precision metal stamping services recommend only progs. To add to all of these points, the speed of the metal stamping presses can be much faster than a tandem or transfer die setup.
III. Transfer Dies in Metal Stamping
Transfer dies are designed to perform multiple operations on a metal sheet in a single pass through a press, with the help of transfer mechanisms. The transfer mechanisms are used to move the metal sheet from one station to the next, where each station is equipped with a different set of tools for performing a specific operation.
Advantages of Using Transfer Dies
Increased efficiency: By performing multiple operations in a single pass through the press, the production process becomes more efficient, reducing the overall time required for each operation.
Improved accuracy: Transfer dies are designed to perform multiple operations in a specific order, with the help of transfer mechanisms, which helps to ensure that the final product is accurate and consistent.
Cost savings: By reducing the number of die sets required, transfer stamping dies can help to lower overall production costs.
Applications of Transfer Dies in Sheet Metal Stamping
Body panel stamping: Transfer dies are commonly used in the production of automotive body panels, where they are used to cut, bend, and form the blank into the desired shape.
Chassis components: Transfer dies can also be used in the production of various chassis components, such as cross members, brackets, and sub-assemblies.
Engine components: Transfer dies are also used in the production of engine components, such as cylinder heads, intake manifolds, and valve covers.
Transfer dies play a significant role in sheet metal parts stamping and provide numerous benefits to manufacturers and suppliers. By performing multiple operations in a single pass through the press, with the help of transfer mechanisms, transfer stamping dies offer increased efficiency, improved accuracy, and cost savings, making them a preferred choice for many applications in the automotive industry.
IV. Compound Dies in Metal Stamping
These dies are a type of die that combines multiple operations into a single die set. This means that instead of having multiple dies for each operation, such as punching, cutting, bending, and forming, the die performs all of these operations in one go. This results in a more efficient and cost-effective process compared to using multiple dies for each operation.
Advantages:
Increased efficiency: By combining multiple operations into a single die set, the production process becomes more efficient and reduces the time required for each operation.
Improved accuracy: Designed to perform multiple operations in a specific order, which helps to ensure that the final product is accurate and consistent.
Cost savings: Reducing the number of die sets required can help lower overall production costs.
Applications:
Body panel stamping: Commonly used in the production of automotive body panels, where they are used to cut, bend, and form the blank into the desired shape.
Chassis components: Can also be used in the production of various chassis components, such as cross members, brackets, and sub-assemblies.
Engine components: Also used in the production of engine components, such as cylinder heads, intake manifolds, and valve covers.
They play a significant role in the steel stamping industry and provide numerous benefits to manufacturers and suppliers. Combining multiple operations into a single die set offers increased efficiency, improved accuracy, and cost savings, making them a preferred choice for many applications in various industries.
V. Fineblanking Dies in Metal Stamping
Fineblanking is a specialized metal stamping process, a precision metal stamping service, that uses a fineblanking die to produce high-precision custom stamped parts with a clean, burr-free edge. The fineblanking process uses a punch and die to shear the metal, resulting in a smoother and more accurate edge compared to traditional stamping processes.
Advantages of Using Fineblanking Dies
High precision: Custom designed to produce high-precision custom stamped metal parts with a clean, burr-free edge, making them ideal for applications where accuracy is critical.
Improved surface finish: Process results in a smoother and more accurate edge than traditional stamping processes, improving the metal parts overall surface finish. This does all depend on die surface finish though.
Reduced secondary operations: The burr-free edge produced by fineblanking reduces the need for secondary operations, such as deburring, which can help to lower overall production costs.
Applications of Fineblanking Dies in Sheet Metal Stamping
Engine components: Commonly used in the production of high-precision engine components, such as valve lifters, camshafts, and bearings.
Transmission components: Are also used in the production of transmission components, such as gears, shafts, and bushings.
Suspension components: Can also be used in the production of suspension components, such as control arms, brackets, and bearings.
They play an important role in the sheet metal stamping industry, providing manufacturers and suppliers with a specialized tool for producing high-precision custom stamped metal parts with a clean, burr-free edge. The high precision and improved surface finish offered by fineblanking dies make them ideal for many industries, where accuracy and quality are critical.
VI. Draw Dies in Metal Stamping
Draw dies are a type of die used in metal stamping to produce parts with a deep drawn or formed shape. The process involves placing a metal blank into a die, then using a punch to force the metal into the die cavity, resulting in the desired shape. The punch also serves to control the metal flow, which helps to ensure that the final part is of the correct size and shape.
Advantages of Using Draw Dies
High-volume production: Custom designed for high-volume production, making them ideal for many industries.
Improved dimensional accuracy: The controlled metal flow in the draw die process helps to ensure that the final part is of the correct size and shape, which is essential for many automotive applications.
Cost savings: The use of draw dies can help to lower overall production costs by reducing the need for secondary operations, such as trimming, that may be required with other stamping processes.
Applications of Draw Dies in Sheet Metal Stamping
Body panels: Commonly used in the production of body panels, such as fenders, doors, and hoods, where they are used to form the metal into the desired shape.
Fuel tanks: Used in the production of fuel tanks, where they are used to form the metal into the desired shape and size.
Engine components: Used in the production of engine components, such as oil pans and transmission casings.
Draw dies are a vital tool in the sheet metal stamping industry, providing manufacturers and suppliers with a means of producing high-volume, high-precision parts with deep drawn or formed shapes. The improved dimensional accuracy and cost savings offered by draw dies make them an important asset for many industries.
VII. Trim Dies
Trim dies are a type of die used in metal stamping to remove excess material from a stamped part. The process involves using a punch to cut or trim the metal along a pre-determined line, resulting in a part that is the correct size and shape. Trim dies are typically used as a secondary operation in metal stamping, following the initial stamping process.
Advantages of Using Trim Dies
Improved dimensional accuracy: The use of trim dies helps to ensure that stamped parts are the correct size and shape, which is essential for many automotive applications.
Reduced scrap: By removing excess material from stamped parts, trim dies help to reduce scrap and improve overall production efficiency.
Increased production speed: Can help speed up the production process by reducing the need for secondary operations, such as hand trimming, that may be required with other stamping processes.
Applications of Trim Dies in Sheet Metal Stamping
Body panels: Commonly used in the production of body panels, such as fenders, doors, and hoods, where they are used to trim the metal to the correct size and shape.
Engine components: Be used in the production of engine components, such as oil pans and transmission casings, where they are used to trim the metal to the correct size and shape.
Suspension components: Trim dies are also used in the production of suspension components, such as control arms and brackets, where they are used to trim the metal to the correct size and shape.
Trim dies play an important role in the Sheet Metal Stamping industry, providing manufacturers and suppliers with a means of improving dimensional accuracy and reducing scrap in the production of stamped parts. The increased production speed and improved efficiency offered by trim dies make them an important asset for many applications in the automotive industry.
VIII. Conclusion
The automotive stamping industry relies on a variety of dies to produce parts for use in vehicles. This article has discussed various types of dies, each of which offers unique advantages and applications in the industry.
The choice of die used in automotive stamping is critical to the success of the production process. Factors such as the size and shape of the part, the required volume, and the desired dimensional accuracy all play a role in determining the best die for a specific application. It is important for manufacturers and suppliers to carefully consider these factors when selecting a die for use in metal stamping.
The field of die technology is constantly evolving, and the metal stamping industry is no exception. New advancements in materials and manufacturing processes are making it possible to produce more complex parts with greater precision and efficiency. In the future, we can expect continued die technology advancements, with new types of dies and improved designs being developed to meet the demands of the automotive industry.
In conclusion, dies play a crucial role in the metal stamping industry, and a careful consideration of the various types of dies and their advantages and applications is essential for success. The continued advancement of die technology will provide new opportunities for manufacturers and suppliers to produce high-quality, high-precision stamped parts for use in vehicles.
Q&A:
What is precision metal stamping?
Precision metal stamping is a manufacturing process that involves punching, cutting, bending, and forming sheet metal material or coils into specific shapes and sizes. The process is typically performed using specialized equipment such as hydraulic presses and progressive stamping machines, and can produce intricate parts with tight tolerances and consistent quality. Precision metal stamping can be used to produce a wide range of products, including automotive parts, electronics components, and consumer goods. The process is often preferred over other metal fabrication methods due to its speed, accuracy, and cost-effectiveness, especially for high-volume production runs. There are many Tool and Die shops that provide precision metal stamping services.
What are the four type of metal stamping?
Pressing blanking, bent coins, embossing and flanging are all methods of stamping. CAD and computer CAM technologies are essential for stamping before they are used to form.
What is sheet metal forming and stamping process?
Sheet metal stamping consists of turning sheet metal into useful parts. The metal is put into the presses where stampers, also called dies, create desired shapes. The metal dies are compressed by tremendous force.
What is the difference between stamping and forming sheet metal?
Stamps can be easily automated and integrated value added procedures like welded or assembled without significantly extending the manufacturing period. Rollforming is an effective technique that lets you combine secondary operations such drilling and cutting into forming.
What is metal stamping vs engraving?
Both are common processes, engraving consists of modification of an object's surfaces and creating customised pieces leaving an attractive smooth and silky feel. Stamps involve hammering the metal to permanent deformation and possibly sharp corners. Engraving is cutting away metal, stamping you are metal forming and displacing steel.
Are stamping dies only for sheet metal parts?
Normally only for sheet metal forming but you can have a stamping die run plastic components or other materials as well. Whatever you are stamping, at whaterver quality level you need, from household appliances to precision projects, you will need punc
What cuts the material thickness in stamping?
Punches or trim steels cut the material. Cutting clearances will be different depending on material type nad thickness. In any die - blanking, or other, you need punches made from hardened tool steel material to punch through the blank material.
What is tool steel?
High carbon ally steel that can be hardened to by made into tools, punches, forms etc.
What are the important factors in blanking dies?
Blanking dies are, as it sounds, tools that are mounted into presses to create precision shapes from blanking out of a coil. Blanking is referring to cutting around a profile surface area. Sometimes they have multiple steps.
What is Tool and Die?
Tools and Die Makers are highly skilled journeymen that create parts and tools made from steel and other specialty materials in various industries. From building custom high precision machined parts to custom niche projects.
What is Quality?
Quality refers to the quality of a components. How to decide on the level of quality of a certain component? In automotive we use GD&T Geometric Dimensioning and Tolerancing which is a three dimensional tolerancing system, making it superior to simple plus and minus tolerancing.
Purpose of Stamping Dies and other precision metal stamping services
The purpose of dies in sheet metal stamping is to provide the necessary force and shape to the metal sheet in order to produce the desired component. Dies are an essential part of the sheet metal stamping process, as they determine the final shape and size of the component. Before the dies do work, you start with flat sheet metal material, and once it runs through the die, you have custom stamped metal parts. To choose what type of die you need, you need to figure out your metal stamping process, the stamping quality desired, and what stamping presses are available for the volume of stamping you need to supply.